Cold Sintering of Calcium Carbonate for Precast Construction Materials
ID# 2020-5045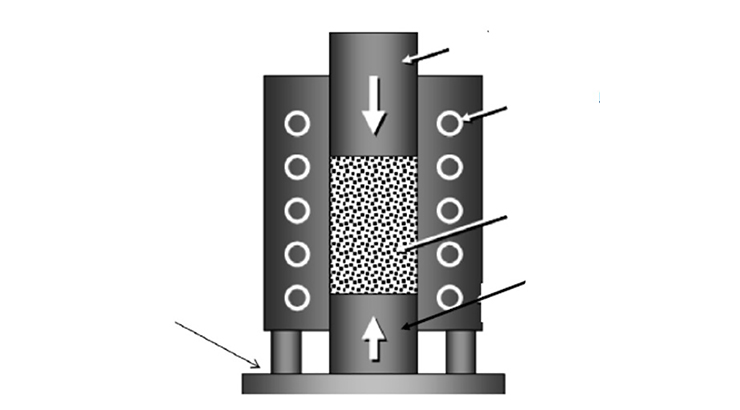
Technology Summary
Conventional construction bricks are manufactured by baking ground raw materials such as clay minerals (kaolin and shale) at temperatures above 1000oC. More sustainable alternatives for ordinary Portland cement (OPC) concrete are desirable, as OPC production accounts for five to eight percent (5-8%) of global CO2 emissions. These emissions occur from the burning of hydrocarbon fuel and the corresponding decomposition of limestone and clay into calcium oxide (CaO) and CO2. Penn State inventors produced precast cold-sintered (~150-300oC) blocks made of a proprietary calcium carbonate composition and wetting agents that were evaluated for grain boundary formation, porosity, compressive strength, and hardness of sample, variations of which showed compressive strengths ranging from 23.6 MPa to 46.3 MPa when fibers were added.
Application & Market Utility
Cold sintering minimizes the energy use associated with conventional high-temperature sintering processes. The technology can provide lower carbon footprint construction material that is fully recyclable compared to existing concrete masonry unit and clay bricks. In addition to improved (i.e., reduced) porosity, higher compressive stress applied during the cold sintering improved the ground calcium carbonate (GCC) hardness values, close to the unhydrated cement grains.
Next Steps
The inventors are continuing their research to determine the correlation between durability and sintering temperature, as well as new applications for the building construction industry.